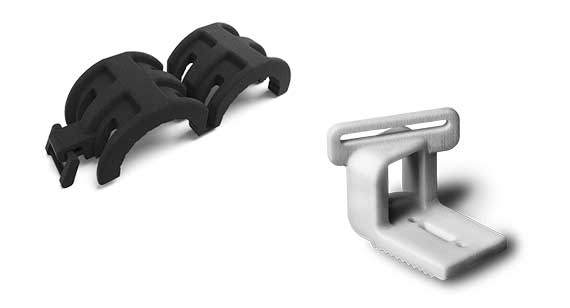
3D printing has revolutionized manufacturing, with various technologies offering unique benefits and applications. Among these, Multi Jet Fusion (MJF) and Selective Laser Sintering (SLS) are two popular additive manufacturing methods. While both utilize powdered materials to produce parts, their processes, advantages, and applications vary significantly. This article delves into the difference between mjf and sls to help you understand which technology might best suit your project needs.
Overview of MJF and SLS
What is MJF?
Multi Jet Fusion (MJF), developed by HP, is an advanced 3D printing technology that uses inkjet arrays to selectively deposit fusing and detailing agents onto a powdered material. A heat source then fuses the powder into a solid layer, building the object layer by layer.
Key Features:
- High-speed production.
- Excellent surface finish and fine details.
- Suitable for functional parts and prototypes.
What is SLS?
Selective Laser Sintering (SLS) uses a high-powered laser to sinter powdered material, fusing particles together to create a solid structure. The laser traces the design layer by layer, forming the part within the powdered bed.
Key Features:
- Versatility in material options.
- No need for support structures.
- Widely used in industrial applications.
Key Differences Between MJF and SLS
- Printing Process
- MJF:Utilizes inkjet technology to deposit agents, followed by a heat source to fuse the powder.
- SLS:Employs a laser to sinter powder directly, layer by layer.
- Material Compatibility
- MJF:Primarily uses polyamide materials like Nylon 12 and Nylon 11. However, its material range is expanding.
- SLS:Supports a broader range of materials, including polyamides, thermoplastics, and composites.
- Speed and Efficiency
- MJF:Faster production due to simultaneous application of fusing agents and heating. Ideal for high-volume production.
- SLS:Slower in comparison, as the laser must trace each layer individually.
- Surface Finish and Detail
- MJF:Superior surface finish and intricate details thanks to its controlled fusing and detailing process.
- SLS:Rougher surface finish that often requires post-processing for smoothness.
- Strength and Durability
- MJF:Produces parts with isotropic properties, ensuring consistent strength in all directions.
- SLS:Offers good mechanical properties but may lack the isotropic strength of MJF parts.
- Cost Considerations
- MJF:Generally more cost-effective for high-volume production due to its efficiency and material usage.
- SLS:More economical for low-volume or specialized material requirements.
Advantages of MJF
- Fast Production:Optimized for quick turnaround times.
- High Detail:Ideal for parts requiring fine details and smooth finishes.
- Cost Efficiency:Minimal material waste and efficient processes lower costs.
- Strong Parts:Isotropic strength ensures durability and reliability.
Advantages of SLS
- Material Versatility:A wide range of materials available for different applications.
- Complex Geometries:No support structures needed, enabling intricate designs.
- Scalability:Suitable for prototypes and small to medium production runs.
- Proven Technology:Widely adopted in industries like automotive and aerospace.
Applications of MJF and SLS
Common Applications of MJF:
- Functional prototypes for consumer electronics.
- Medical devices requiring precision and strength.
- Automotive parts with intricate designs.
Common Applications of SLS:
- Aerospace components with complex geometries.
- Low-volume production of specialized industrial parts.
- Functional prototypes for engineering and testing.
Choosing Between MJF and SLS
Factors to Consider:
- Project Volume:
- Choose MJF for high-volume production.
- Opt for SLS for low to medium-volume projects.
- Material Needs:
- If your project requires specific materials, SLS offers more variety.
- For general applications with polyamides, MJF is an excellent choice.
- Budget Constraints:
- MJF is cost-effective for bulk production.
- SLS may be more economical for specialized, smaller projects.
- Part Requirements:
- MJF excels in precision and surface quality.
- SLS is better for complex designs with no support structures.
Future Trends in MJF and SLS
- Material Advancements:Both technologies are expanding their material portfolios, allowing for broader applications.
- Increased Automation:Automation will enhance efficiency and reduce costs further.
- Sustainability:Innovations in recycling and eco-friendly materials will make these technologies greener.
Conclusion
Understanding the difference between MJF and SLS is crucial for choosing the right 3D printing technology. While MJF offers speed, precision, and isotropic strength, SLS provides material versatility and design flexibility. By evaluating your project requirements, budget, and production goals, you can leverage the strengths of these technologies to achieve optimal results.